How to solve the corrosion problem of metal baler?
Last week we just exported 3 vertical metal balers to India. So why do customers still choose us after comparing multiple products? Excluding these decisive factors such as product quality and machine price, I think the reason why we can succeed is that we pay attention to details.
There is an old saying in China that is good, “Details determine success or failure.” Today we will talk about one of the details of the metal baler, that is how to do a good job of anti-corrosion of the metal baler?
Scrap aluminum metal balers are generally used to process various waste metal raw materials, such as aluminum cans, iron wires, copper wires, iron sheets, copper sheets, and so on. These wastes are sometimes mixed with liquids such as water and chemicals. These liquids will cause some corrosiveness to the machine.
So how can we improve the corrosion resistance of metal balers?
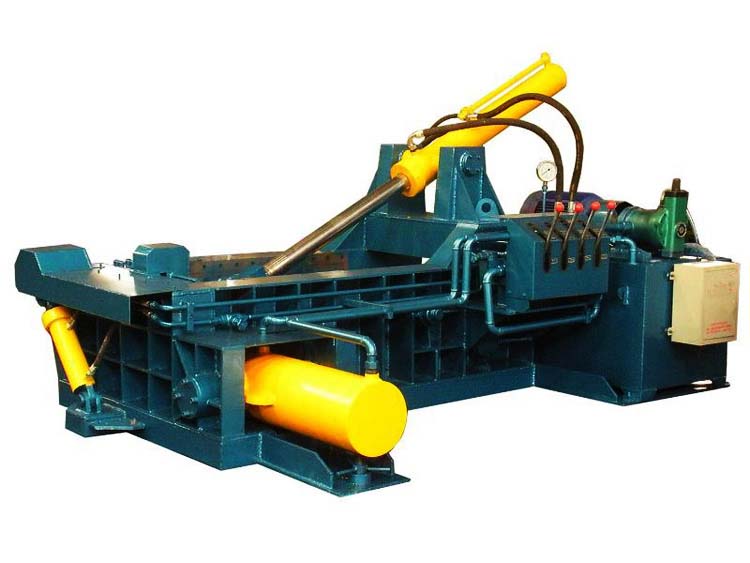
First, the material problem. We use corrosion-resistant metal materials to make the machine to ensure that no corrosion will occur in long-term contact with water.
Secondly, the coating problem. Many manufacturers do not value coatings. Indeed, for some customers, the materials they handle do not contain substances that can cause corrosion. However, if you can’t test one by one for the materials you deal with or the content is uncertain, a certain corrosive coating is necessary. The coatings we use can resist static corrosion, salt, sulfur corrosion, low concentration acid, and alkali corrosion, etc.
In addition, it can also play a protective role on the machine, with a smooth coating surface to prevent scratches. Details not only determine the quality of a machine but also play a decisive role in the success and failure of an enterprise. If you have special requirements and want to customize it. Then you can also contact our customer service to express your requirements.